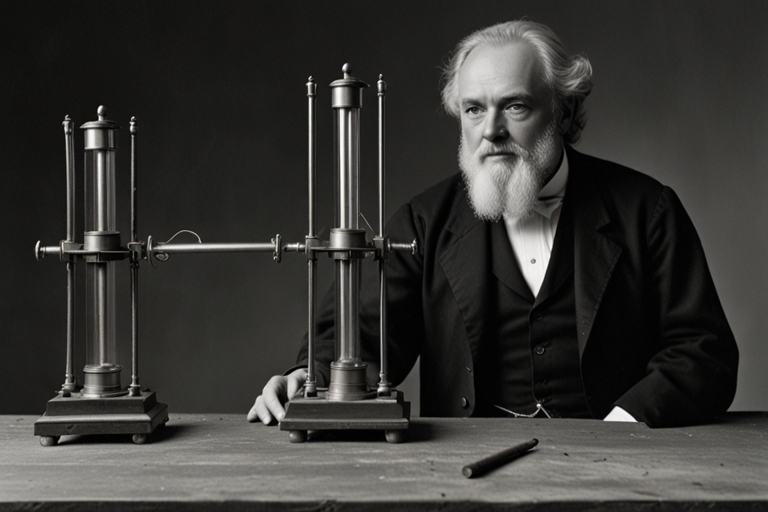
Introduction
Torsion is a pivotal concept in mechanics, offering insights into the behavior of cylindrical objects under twisting forces. Extending the foundational derivations, we can delve deeper into the nuances of torsion, examining its theoretical frameworks, practical applications, and advancements in computational analysis. This article expands on the fundamental principles discussed earlier, bringing to light additional aspects of the torsion of a cylinder derivation and its significance.
Historical Background of Torsion Analysis
The study of torsion dates back centuries, with pioneers such as Galileo and Coulomb laying the groundwork for understanding material deformation. Coulomb’s early experiments in torsion pendulums were foundational in linking torque and angular displacement, forming the basis for modern torsion theories. Over time, these principles have been refined, incorporating advanced mathematical tools and experimental techniques.
Theoretical Derivation: An In-Depth Exploration
The derivation of torsion in a cylinder integrates concepts from material science, geometry, and physics. Let us expand on each derivation step to achieve a more comprehensive understanding.
1. Stress-Strain Relationship in Torsion
Shear stress (τ\tauτ) and shear strain (γ\gammaγ) are fundamental to torsion analysis. The relationship between these quantities for a linear elastic material is given by:
τ=G⋅γ\tau = G \cdot \gammaτ=G⋅γ
Here, GGG represents the shear modulus, a measure of the material’s rigidity. This relationship assumes the material behaves elastically, returning to its original shape once the torque is removed.
2. Angle of Twist Revisited
The angle of twist (θ\thetaθ) can be expressed more generally by integrating the local deformation across the cylinder’s length. The incremental twist dθd\thetadθ over a small length dxdxdx is:
dθ=TG⋅J⋅dxd\theta = \frac{T}{G \cdot J} \cdot dxdθ=G⋅JT⋅dx
Integrating this over the cylinder’s total length L, we find:
θ=∫0LTG⋅Jdx=T⋅LG⋅J\theta = \int_0^L \frac{T}{G \cdot J} dx = \frac{T \cdot L}{G \cdot J}θ=∫0LG⋅JTdx=G⋅JT⋅L
This expression highlights how material properties (GGG), geometry (JJJ), and applied torque (TTT) collectively determine the angle of twist.
3. Strain Energy in Torsion
Torsion induces strain energy within the material, which is the energy stored due to deformation. For a differential element, the strain energy density is:
u=τ22Gu = \frac{\tau^2}{2G}u=2Gτ2
The total strain energy (U) in the cylinder is obtained by integrating over its volume (VVV):
U=∫Vτ22GdVU = \int_V \frac{\tau^2}{2G} dVU=∫V2Gτ2dV
By substituting τ=T⋅rJ\tau = \frac{T \cdot r}{J}τ=JT⋅r and integrating, the strain energy for a solid cylinder becomes:
U = T2⋅L2G⋅JU = \frac{T^2 \cdot L}{2G \cdot J}U = 2G⋅JT2⋅L
This energy is crucial in understanding material behavior under repeated or dynamic loading conditions.
Extensions of Torsion Analysis
Hollow Cylinders and Thin-Walled Tubes
For hollow cylinders, the derivation modifies the polar moment of inertia (JJJ) to account for the inner and outer radii (rir_iri and ror_oro):
J=π(ro4−ri4)2J = \frac{\pi (r_o^4 – r_i^4)}{2}J=2π(ro4−ri4)
For thin-walled tubes, where ro−rir_o – r_iro−ri is small compared to ror_oro, an approximation simplifies JJJ:
J \approx 2 \pi r_m^3 tJ ≈ 2πrm3t
Here, rmr_mrm is the mean radius, and it is the wall thickness. Thin-walled approximations are particularly useful in aerospace and automotive engineering, where lightweight structures are paramount.
Non-Circular Cross-Sections
While cylinders typically have circular cross-sections, other geometries (e.g., square, rectangular, or elliptical) exhibit distinct torsional properties. For non-circular sections, the torsion constant (CtC_tCt) replaces JJJ in calculations, and warping effects must be considered.
For a rectangular cross-section of width B and height, he:
Ct=13bh3 (for b>h)C_t = \frac{1}{3} b h^3 \text{ (for } b > h \text{)}Ct=31bh3 (for b>h)
Advanced computational methods, such as finite element analysis (FEA), help analyse complex cross-sections more accurately.
Advanced Topics in Torsion
Dynamic Torsion
When a cylinder is subjected to time-varying torque, dynamic effects like resonance and damping become significant. Torsional oscillations have the following equation of motion:
I⋅d2θdt2+c⋅dθdt+k⋅θ=T(t)I \cdot \frac{d^2 \theta}{dt^2} + c \cdot \frac{d\theta}{dt} + k \cdot \theta = T(t)I⋅dt2d2θ+c⋅dtdθ+k⋅θ=T(t)
Here:
- III: Moment of inertia of the rotating mass.
- Ccc: Torsional damping coefficient.
- kkk: Torsional stiffness (k = GJ/Lk = GJ/Lk = GJ/L).
- T(t)T(t)T(t): Applied torque as a function of time.
Dynamic torsion analysis is crucial in rotating machinery, such as engines and turbines, where oscillatory forces are prevalent.
Plastic Torsion
Materials often exceed their elastic limits in real-world applications, entering the plastic deformation regime. Plastic torsion theory accounts for non-linear stress-strain behavior. The Tresca and von Mises yield criteria are commonly used to predict failure under torsion.
Material Considerations in Torsion
Impact of Material Properties
The performance of a cylinder under torsion depends heavily on its material properties:
- High Shear Modulus: Materials with high GGG (e.g., steel, titanium) resist torsional deformation effectively.
- Fatigue Resistance: Repeated torsional loading can lead to fatigue failure, making materials like alloys and composites ideal for high-cycle applications.
Anisotropic Materials
In anisotropic materials (e.g., composites), properties vary with direction, complicating torsion analysis. For these materials, tensors describe the relationship between stress and strain.
Real-World Applications of Torsion
1. Power Transmission
Cylindrical shafts in engines, turbines, and gear systems are designed using torsion principles to ensure efficient power transmission without failure.
2. Torsion Springs
Torsion springs, used in clocks, door hinges, and suspension systems, store energy by twisting. Their design leverages the torsion of a cylinder derivation to optimize energy storage.
3. Biomedical Devices
The material’s theoretical properties are crucial in designing surgical instruments, orthopedic implants, and prosthetics. Cylindrical rods used in spinal surgeries, for instance, must withstand torsional loads without failure.
4. Construction and Infrastructure
Torsion is vital in analyzing beams, bridges, and pipelines, ensuring structures can withstand twisting forces due to wind, earthquakes, or operational loads.
Torsion Testing Techniques
1. Torsion Pendulum Test
This test, used to measure the shear modulus of materials, involves oscillating a cylindrical specimen and analyzing its angular frequency.
2. Static Torsion Test
This involves applying incremental torque to a specimen and measuring the resulting angle of twist and shear stress.
3. Dynamic Torsion Test
Dynamic tests simulate real-world loading conditions, providing insights into fatigue behavior and failure mechanisms.
Advancements in Computational Analysis
The advent of computational tools has transformed torsion analysis, enabling the simulation of complex scenarios:
Finite Element Analysis (FEA)
FEA divides the cylinder into small elements, solving torsion equations for each element to provide detailed stress and strain distributions.
Machine Learning and AI
Artificial intelligence algorithms predict torsional behavior in complex systems, optimizing designs and reducing computation time.
Case Studies in Torsion
1. Failure Analysis of a Steel Shaft
A steel shaft in a power plant experienced catastrophic failure due to excessive torsion. Post-mortem analysis revealed stress concentrations at a keyway, highlighting the importance of geometry in torsion design.
2. Optimization of Composite Drive Shafts
In the automotive industry, composite materials are replacing steel for drive shafts. Using FEA, engineers optimized these components’ torsional strength and weight, improving vehicle performance.
Challenges in Torsion Analysis
Despite advancements, torsion analysis faces challenges:
- Complex Geometries: Non-uniform cross-sections require advanced mathematical and computational techniques.
- Temperature Effects: High temperatures alter material properties, affecting torsional behavior.
- Multi-Axial Loading: Real-world scenarios often involve combined axial, bending, and torsional loads, complicating analysis.
Future Directions in Torsion Research
Smart Materials and Structures
The development of smart materials that adapt to torsional loads dynamically is a promising field. Shape-memory alloys and piezoelectric materials are leading the way.
Nano-Scale Torsion
At the nanoscale, torsional behavior deviates from classical theories, requiring quantum and molecular dynamics simulations.
Conclusion
The torsion of a cylinder derivation forms the backbone of numerous engineering applications, from machinery to infrastructure. By expanding its theoretical and practical aspects, engineers and researchers continue to push the boundaries of material science and structural analysis.